BUILDING A SUSTAINABLE FUTURE: 2020-BEYOND
How do you get plants and offices around the world on the same page when it comes to process?
There’s no one-size-fits-all approach, but the Sonoco Performance System (SPS) has helped us ensure that every team—regardless of location—can aspire to world-class operations.
Maintaining universal standards for efficiency, safety and quality in Sonoco locations around the world is a challenge, to say the least. Supply chains are always shifting, impacted by local and global markets. Technology and regulations vary from region to region. And teams in different places are influenced by different cultural nuances.
In 2010, we introduced SPS as a way of standardizing processes and a rallying cry for our plants around the world.
Its objectives include:
- Improving safety.
- Supporting growth and our relationship with customers.
- Allowing more time to focus on productivity and process improvement.
- Optimizing a more flexible workforce to meet challenging business demands.
- Creating a culture of clearly aligned metrics, accountability and process.
In 2010, our goal was a 3.5% annual improvement in manufacturing productivity. We piloted SPS at the paper mill and two Tubes & Cores (T&C) converting plants in Newport, Tennessee. That same year, one of those T&C plants managed to reduce scrap by 40% from what we’d previously thought to be the highest possible performance.
In 2012, Waco, Texas, served as the pilot plant for the Flexibles division. By 2015, they had reached Gold status through far fewer returned sales, internal waste, downtime and other key metrics. Waco was the first Gold plant in the entire company to be recertified without any contingencies.
As of 2021, more than 100 facilities have been involved in the SPS certification process. In the Asia-Pacific (APAC) region alone, “there are nine plants currently on the SPS journey,” according to Alvaro Razquin, General Manager & Vice President, Global Paper Products in APAC.
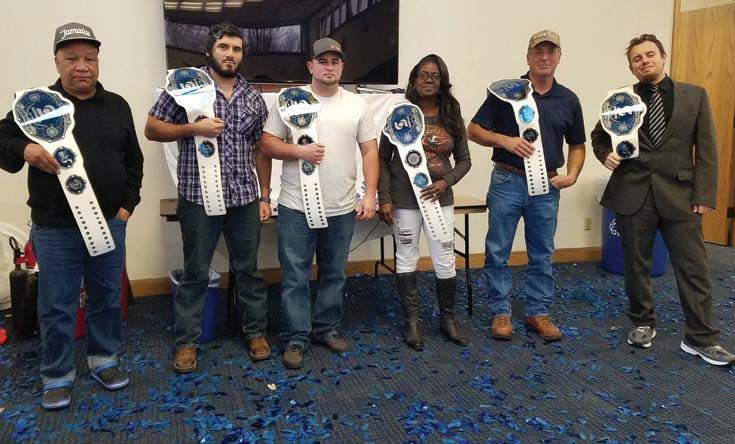
SPS is a driving force in “creating and sustaining Sonoco’s cultural attributes in all [our] premises and footprints globally,” says Alvaro. He’s observed that the more a shop floor adheres to the SPS philosophies, the more productive and safe working conditions can be.
SPS has been so successful that teams have started exploring how we can apply similar systems elsewhere across the business. Chief Operating Officer Rodger Fuller asks, “How do we take things like the Sonoco Performance System, which is focused on continuous improvement, and drive that through all the staff functions, organizations like HR, finance and IT?”
Sonoco Performance System is a worldwide measuring stick. It’s our ultimate tool to standardize safe, efficient practices and equip teams to be nimble and adaptable, always delivering world-class services and products for our customers around the globe.