PLANTING OUR ROOTS: 1899-1969
People know Sonoco for many things: operational excellence across a global supply chain, dependable customer service, mission-driven sustainability, collaborative innovation and more. None of these things would have stood the test of 125 years without our commitment to pursuing world-class safety.
Throughout the last century, many manufacturers have grappled with maintaining safety standards throughout the ebbs and flows of production. Sonoco was no exception.
During World War II, the U.S. became the “arsenal of democracy” in the global fight against fascism. Production boomed across American industry. The government set impressive targets: for example, a threefold jump up to 60,000 aircraft needed in 1942, doubling again to 125,000 the next year. That rush sometimes meant factories were working three shifts around the clock—increasing the risk of accidents. We had to figure out how to stay safe while increasing production.
To prevent safety incidents, Sonoco launched a contest for all employees: The winning department was the one with the lowest percentage of employee hours lost to accidents.
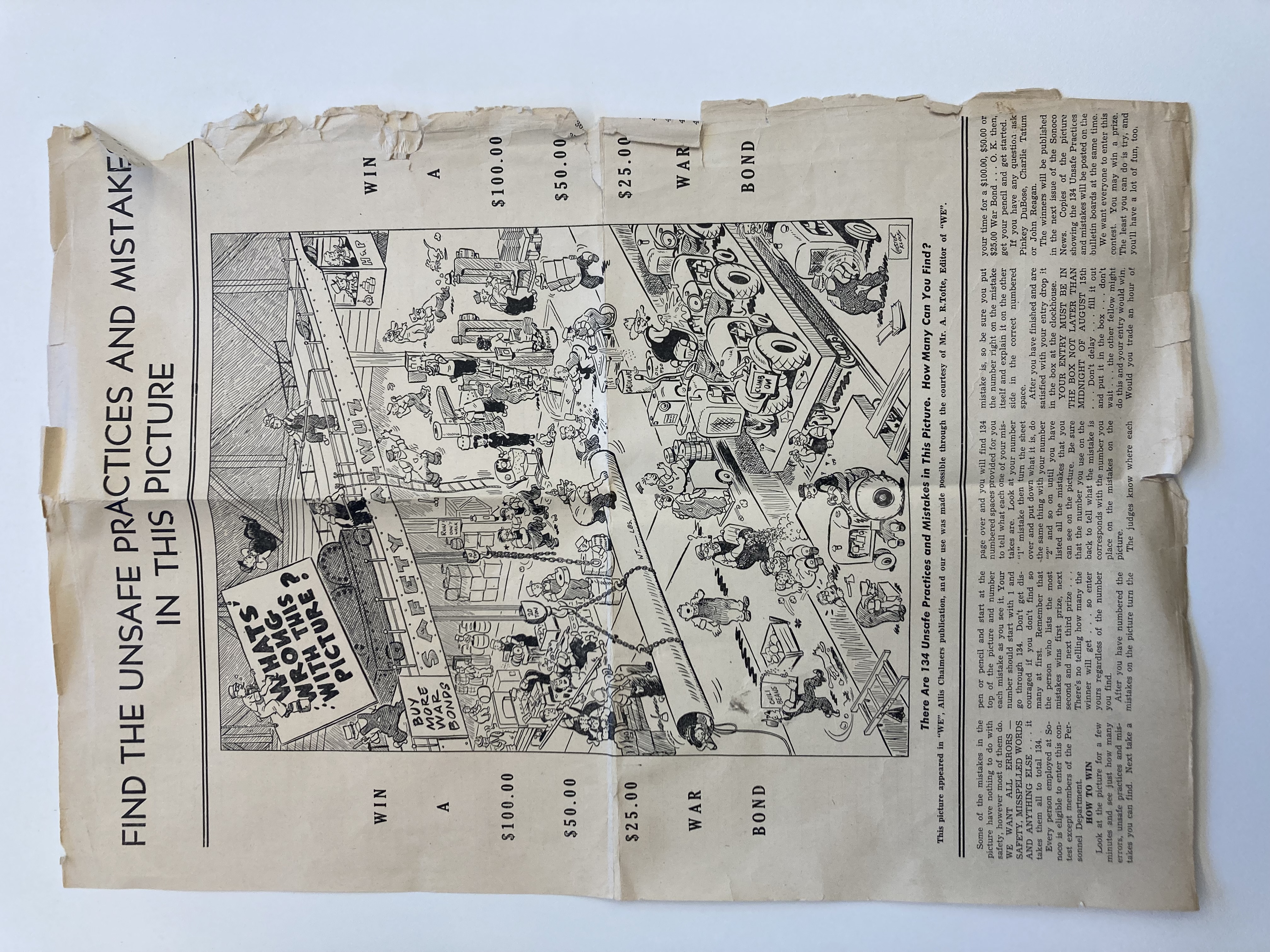
But that was just the beginning. Next, we shared another contest with employees in the summer of 1944. Clipped from the catalog of Allis-Chalmers, a tractor manufacturer that, like so many others, turned to defense manufacturing during the war, the contest challenged staff members to sharpen their safety eyes: “Find the unsafe practices and mistakes in this picture.”
The drawing featured 134 unsafe practices to avoid, including fighting coworkers and bringing pets to the workplace. Employees pored over the picture and then numbered every mistake from top to bottom. They could check their answers against the full list on the back of the page.
The reward? A chance to win war bonds that paid off in denominations of $25, $50 or $100. Our teams competed to show off their safety knowledge, and their winnings supported the war campaign—a win-win.
After the war, our drive for safety took a new turn. Some of the safety gains we had tested became long-term policy. For example, Sonoco’s Safety Committee met in February 1946 and reviewed the recommendation of a subcommittee that had convened “to study the safety goggle situation.”
While tracking industry accident rates and making improvements accordingly, we had noticed that factories that established a safety eyewear policy showed a significant downturn in eye injuries. As a result, our safety team recommended goggles for as many employees as possible. Employees who wore eyeglasses could get prescription safety goggles—at no cost to them.
Sonoco’s efforts for worker safety also devoted attention to veterans returning home and reentering the civilian workforce. At the Southern Safety Conference held in Winston-Salem, North Carolina, in March 1946, Assistant Personnel Director D.A. Bramlett gave a talk on “Safety and the Returning Veteran.”
We also helped standardize other safety practices, including the use of colors in our facilities to signal safety messages, a system now used across America in various industries. In the spring of 1946, Sonoco adopted the American Standards Association for Manufacturing Plants’ recommended color standards. Green indicated safety and first aid equipment, while yellow signage signaled hazards and alerted workers to edges or steps. Many of these early practices worked so well that they remain in place today, keeping employees safe.
As we expand our global presence, our commitment remains the same: building our businesses by doing the right thing. We’ll keep our employees safe while helping our customers meet their production needs and sustainability goals with dependable service and collaborative innovation for the next 125 years and beyond.